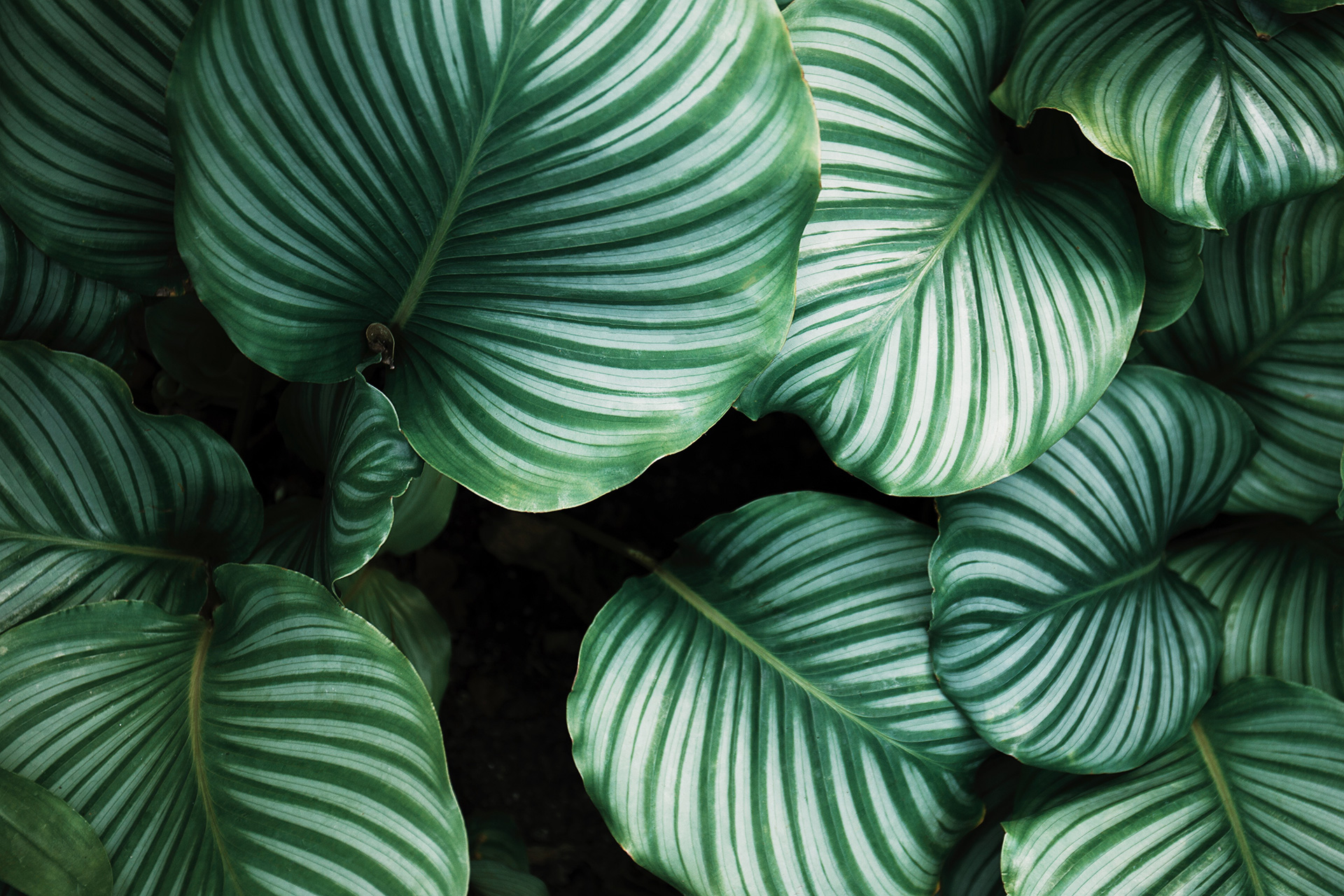
MECHANICAL RISK IN THE MACHINERY DIRECTIVE
There is always a tendency to underestimate the risk that a machine can create, as a result we see many people, for example, detaching safety micro switches and carrying them in their pockets. Many decide to do it their way, because they think they have reasoned better than the machine manufacturer. Those who build machinery must think about the safety of the operators and protect them from Mechanical Risks. For example, it is necessary to ensure that those who use the machine do not crush their hand in the middle of the gears, or that they do not get caught. In theory, the worker should not wear bracelets, rings and anything that can get caught, but it is always better to foresee these situations. The Technical Standards require that common sense be used. Furthermore, it is necessary to foresee easily predictable incorrect use. Mechanical Risks can be crushing, entanglement, shearing, cutting, sharp edges, burred sheet metal, etc. Risks also include falling, which is more likely to occur at height, but can also happen in other circumstances. In addition, there are Derivative Risks, which are those from expulsion, for example if while a machine is working, a bottle breaks and explodes, sending out pieces of glass. The Machinery Directive lists the RES, essential safety requirements, but not the details on how to comply with them. The Technical Standard provides the details, but it is not always applicable. The Machinery Directive states that a risk is avoidable and better resolved if it is done in the design phase. If you realize that the accident prevention protection you are designing has obvious gaps, from the point of view of the physical protection of the operator, you must take charge of it. Even if after an accident it is demonstrated that the operator had been perfectly trained, the accident demonstrates that something did not work.
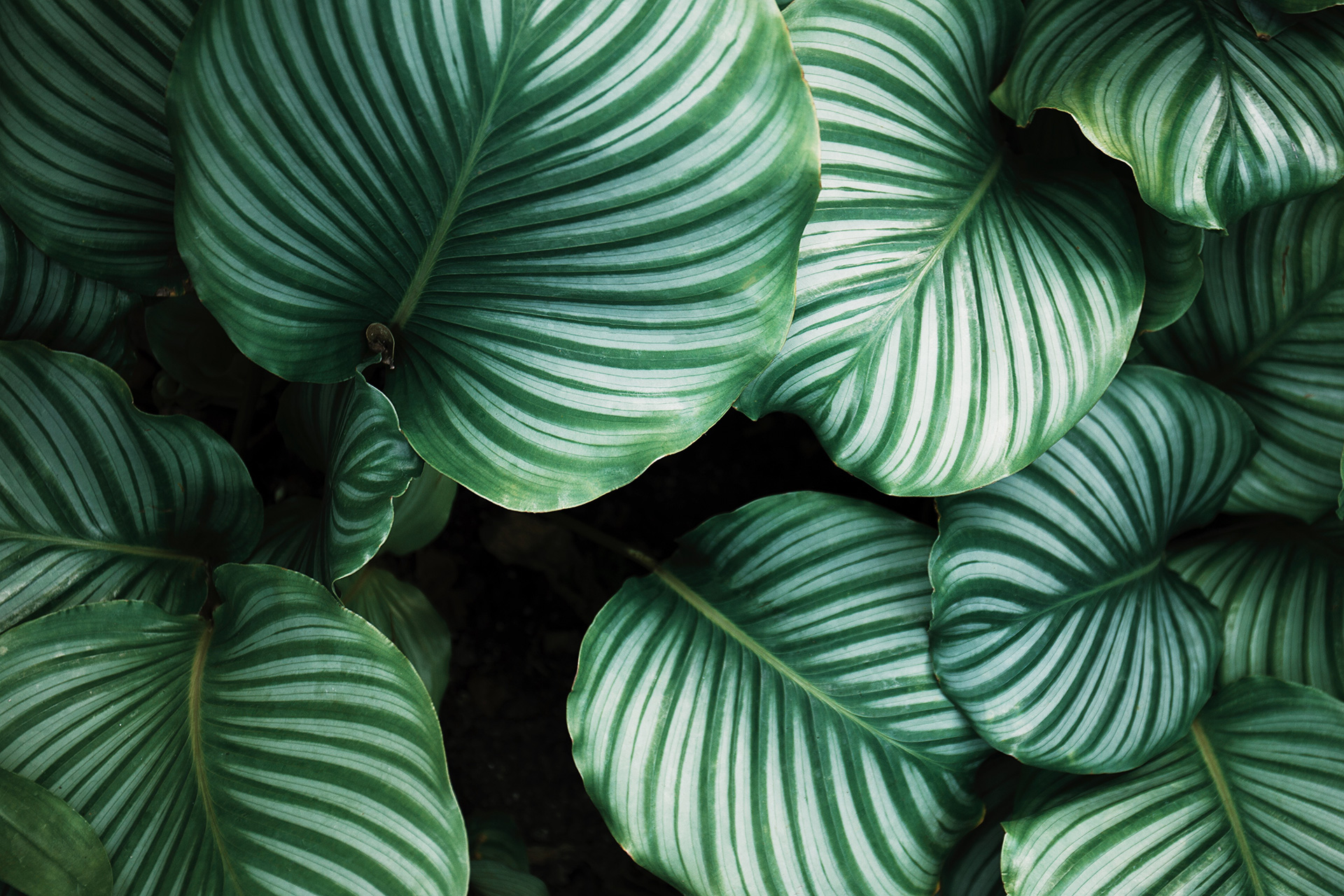
SHOULD MACHINE GUARDS BE CE CERTIFIED? UNI EN 14120
When I buy a machine, the Declaration of Conformity of the machine also includes the guards. If I then buy a guard from the machine manufacturer as a spare part, that guard will not have the CE as it is included in the certification of the machine. If, however, I buy a guard individually as a safety component, according to the Machinery Directive it must be CE certified. It is called a “safety component” as it protects a person from getting hurt. In Annex V of the Machinery Directive there is a list of all the Safety components. There is a Technical Standard that indicates how to make the guards, providing all the necessary parameters, the 14120:2015.
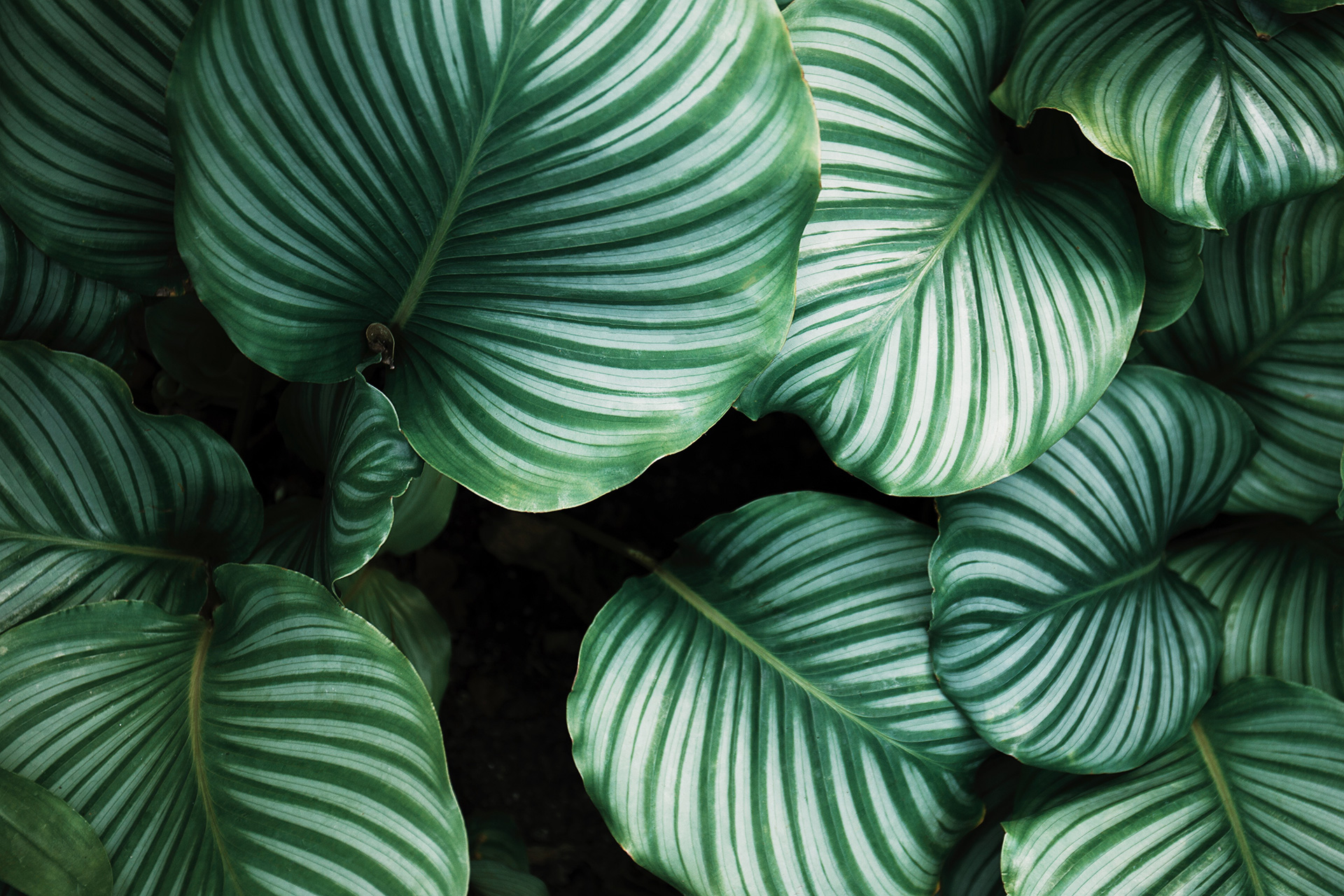
IS EN 14120 MANDATORY FOR FIXED SHELTERS? HOW DO I CERTIFY THEM?
There is only one Technical Standard to comply with, EN 14120, but it is not mandatory to comply with it. However, it is mandatory to comply with the Machinery Directive, which was implemented by Legislative Decree 17/2010 and is a binding standard. For example, the RES, Essential Safety Requirement Machinery Directive 1.3.7, specifies that I cannot come into contact with moving parts, but not how. The Technical Standards are only a way of complying with the Machinery Directive, so it is possible to self-certify that you comply with it. If, however, you do not want to take on this responsibility, buy the Standard on the UNI website, where it is written how the protection must be made. It is therefore designed based on what is written in the Standard. If you comply with the Standard, you have the Presumption of Conformity, which means that you have done the best you can. While if you do not comply, they can tell you that you have not complied with it in order to save money and you will have to demonstrate that you have carried out the analysis of all the risks. If you respect the Standard, the analysis has already been done by whoever wrote it and by respecting it you have done what was required of you.
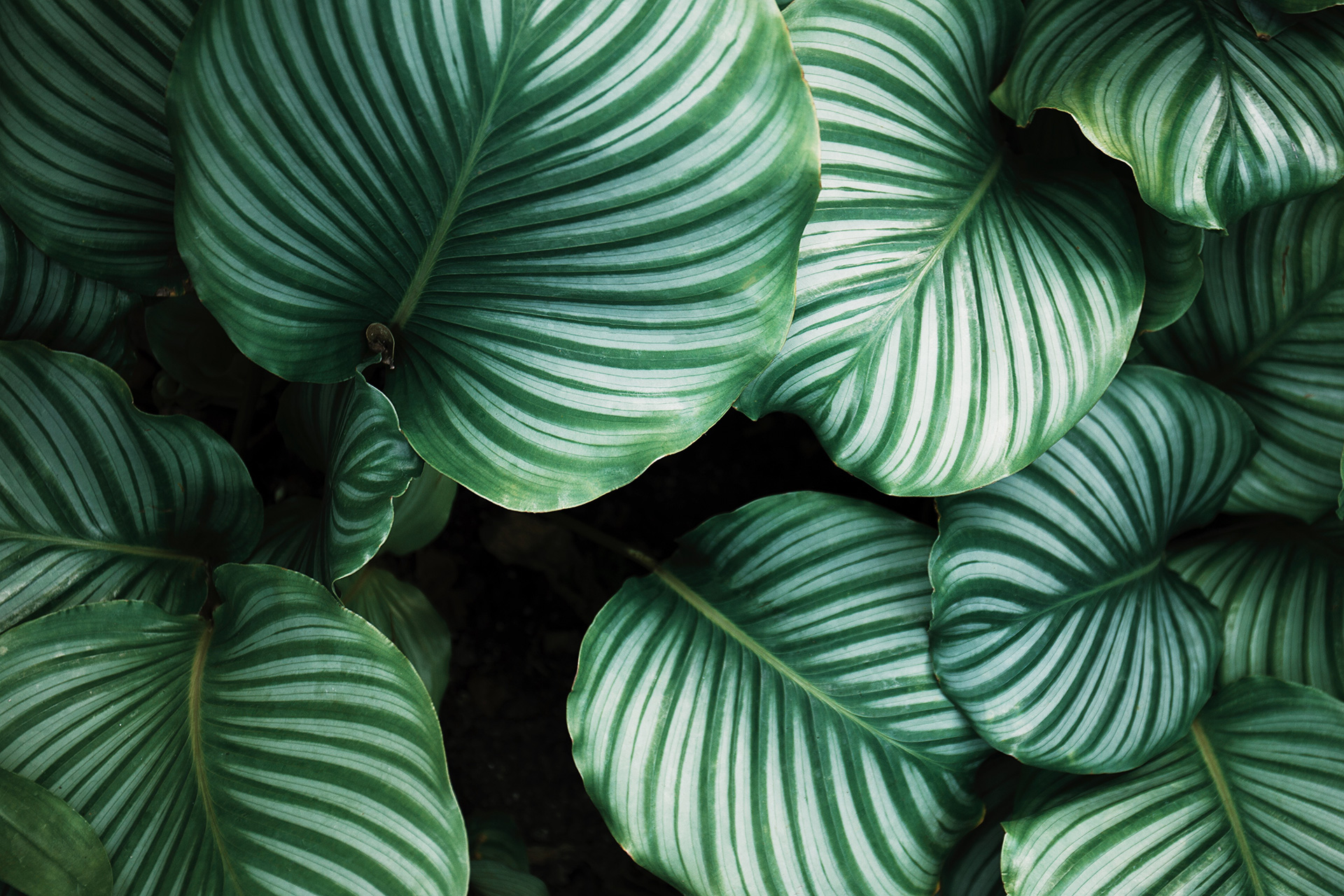
RSPP HSE AND FIXED SHELTERS: WHAT SHOULD THEY LOOK AT?
First of all, you need to check if the protections that the manufacturer has chosen are suitable for you. Since the CE is a self-certification, it does not mean that you agree with the Declaration of Conformity signed by the manufacturer. It could be that you detect obvious risks, in which case you need to contest them with the manufacturer. For example, it is not possible to accept that a worker can put his hand inside moving parts. The first check to do is therefore to see if the machine is suitable for you, and this is not a given. Then you need to check if what is written in the manual coincides with the machine delivered. Because sometimes the Manual is written by an external company, or it is a copy and paste, or often a Manual is made for many machines. It is not a given that the Manual is precise, you need to read it to see if what is written corresponds to the machine. Finally, periodic checks must be done. As the machine is used, perhaps the interlocks are bypassed, or the Carters are dismantled and not reassembled. It is necessary to check periodically, if everything is there it shows that you have checked. Or if something is missing it must be reported and a sanctioning system can be activated. You can send a letter to the worker or verbally reprimand him. A good RSPP checks periodically. Recording when the protections are present or not in an accident trial can be useful as it is objective evidence that the protections were present or not that day. It shows attention and constant verification of the protection devices. Let's give some examples of what you need to look for and watch when looking at a machine. First of all, you need to check if the protections that the manufacturer has chosen are suitable for you. Since the CE is a self-certification, it does not mean that you agree with the Declaration of Conformity signed by the manufacturer. It could be that you detect obvious risks, in which case you need to contest them with the manufacturer. For example, it is not possible to accept that a worker can put his hand inside moving parts. The first check to do is therefore to see if the machine is suitable for you, and this is not a given. Then you need to check if what is written in the manual coincides with the machine delivered. Because sometimes the Manual is written by an external company, or it is a copy and paste, or often a Manual is made for many machines. It is not certain that the Manual is precise, you have to read it to see if what is written corresponds to the machine. Finally, periodic checks must be done. As the machine is used, perhaps the interlocks are bypassed, or the Carters are dismantled and not reassembled. It is necessary to check periodically, if everything is there it is demonstrated that it has been checked. Or if something is missing it must be reported and a sanctioning system can be activated. You can send a letter to the worker or reprimand him verbally. A good RSPP checks periodically. Recording when the protections are present or not in an accident trial can be useful as it is objective evidence that the protections were present or not that day. It shows attention and constant verification of the protection devices. Let's give some examples of what you need to look for and watch when looking at a machine.
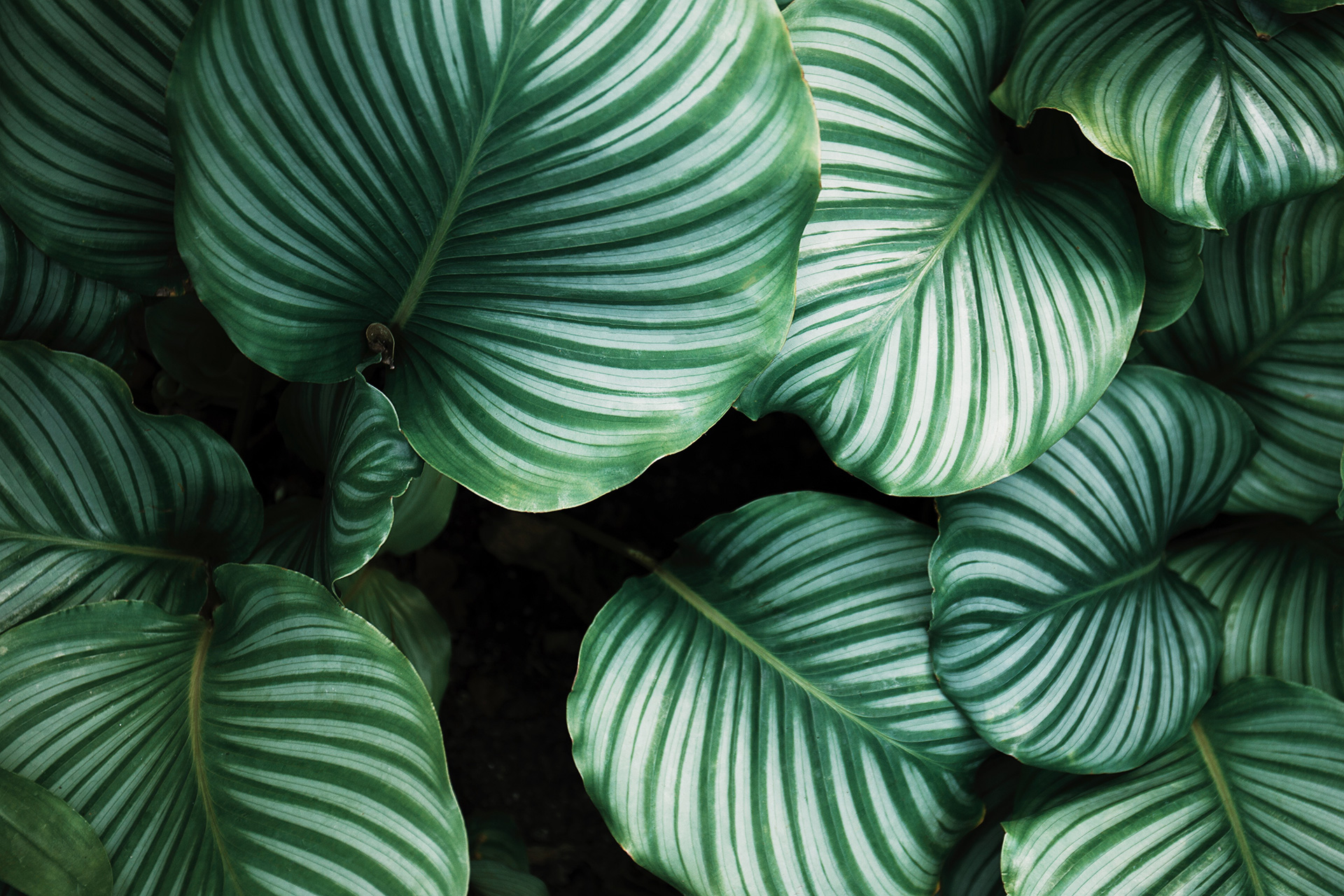
What you need to know
"CE" MARKING ON THE PROTECTIONS OF A MACHINE – IS THERE A PLATE? When you sell a machine, the buyer trusts that it is safe and compliant with all the rules. The seller of the machine does not build it all, but assembles the pieces from various suppliers. Let's say you make the protections and fixed guards that are attached to the machine, such as the perimeter ones which are protections that delimit a perimeter beyond that of the machine itself. The manufacturer of the machine, in order not to take on your responsibilities, asks you to certify what you sell him. It is a legal requirement, if you sell a safety component it must be CE marked according to the Machinery Directive. If the manufacturer sells a machine already with the protections, these are not certified because they are part of the machine as a whole. But if you sell only a component with a protective safety purpose, according to the Machinery Directive it must be CE marked. This is a very important thing to know, especially when ordering, to prepare the documentation to give to the customer, such as the CE Plate. If I am a machine builder and I buy the perimeter guards from you, I will put your Manual, your CE Plate and your Declaration of Conformity in my Technical File. If I make the perimeter guards myself, I will have my drawings and my calculations, which I will put in my Technical File. FIXED AND MOVABLE GUARDS: HOW DO I CHOOSE THEM? There are two types of guards. There is the physical one, I physically prevent the operator from reaching the machine in operation, such as fixed guards and interlocked guards. Or it is possible to detect an intrusion into the danger zone using optical barriers and laser scans in such a way as to prevent the production process from continuing. A special case is the Carter with safety interlock, which when removed stops the entire machine. This prevents the maintenance technician from operating the machine without restoring the guard. In this way, without the Carter the operator can access the danger zone of the machine, but since it is stationary he is not in any danger. Remember that a Carter must be immediately recognizable when it is disassembled, to leave it disassembled there must therefore be intentionality, or laziness. So how do I choose when to put a carter, an interlocking door or a laser scan? I choose it based on the use that the operators make of it and what they have to do to work. If the maintenance worker has to access the machine once a month, a fixed Carter with 4 bolts is more than fine. If instead he has to, for example, clean a roller with a solvent and has to do it every 8 hours, a fixed Carter tends not to be reassembled every time, out of laziness. In this case it is possible to put an Interlocking Door, so that when it is opened the machine stops. In reality, the machine should be stopped first and then the door opened, but not all of us are so diligent, the interlocking door is used to avoid forgetting. If, on the other hand, the worker has to access the machine several times during the shift, even the Interlocking Door can be an obstacle. You can therefore install an Optical Barrier, which however requires certain spaces. The Optical Barrier also needs Buffer Zones, areas in which it is not possible to touch the machine. There must be a distance between the operator and the danger, so as to give the machine time to stop, because on some types of machines the stop is not immediate. A 500 kg reel does not stop instantly, there is a stop time to check. There are also Interlocked Carters, the interlock ensures that the machine does not restart until the Carter has been repositioned, but not all Carters need them. The Fixed Interlocked Carter is a very little used system, as each interlock costs money and is a possible source of failure. It is the manufacturer of the machine who must decide whether or not to install it. It is installed if there are particularly dangerous points in which it is known that the operator tends to leave the Carter removed and this risk cannot be run. Hinged guard? is it fixed or mobile? We received this question from a court expert who found himself in front of a guard attached to the machine on the right side by a hinge and on the left side fixed with a bolt. The answer lies in the problem it has to solve and the result you want to achieve. As stated in par. 6.3.2 of EN 12100: a fixed guard is used if access to the danger zone is not required in a “normal” situation. That is, it is unavoidable to access that zone with a high frequency. In that case it is better to use an interlocked movable guard. If I put a fixed guard it means that it can/must be removed only a few times, not frequently. Only for maintenance, cleaning, etc. Instead, a movable guard - to be functional - should be interlocked when opened, and frequently. Otherwise it becomes ineffective. If I put a fixed guard, for a serious unacceptable risk, I must ensure that it is put back in position before starting. What happens if they forget it somewhere? For example, a fixed guard to protect the grinding parts... A grid... if I don't install them... everything works the same. This way the operator is more comfortable in the event of a "clogging", he might not stop the crusher, and intervene with a tool such as a lever. There are examples of seriously incorrect behavior... easily predictable. So: The fixed guard should be "attached" in an obvious way to the area to be protected, even if removed. A chain? A hinge? This way you can see that... it's dangling and missing (for example). Obviously, if removed, it must not remain in position if only supported. It must be fixed. Otherwise it must be interlocked. Even EN ISO 12100, in par. 6.3.3.2.2 (requirements for fixed guards) provides for the hinge as a possibility. CARTER: WHAT IS IT? WHEN IS IT USED? HOW IS IT USED? The Carter is a fixed protection, an accident prevention guard. In a safety device designed to protect the operator from mechanical risks, the Carter is a means that comes between the operator and the danger. It does not matter what material it is made of, but what counts is its function, which is to protect the operator. Since it is fixed, it must not be possible to disassemble it. Therefore, there must not be wing nuts that can be easily unscrewed by hand, but must be able to be unscrewed only through the use of certain tools. You must have full intention to disassemble a Carter, at your own risk. HIGH VISIBILITY PROTECTIONS WHAT ARE THEY? – MACHINERY DIRECTIVE With the same type of machines to protect, there are customers who want a lot of brightness, therefore a lot of transparency. In those cases, also based on the product they will be treating, glass or polycarbonate, always transparent, will be used for the protections. What is the difference between the two? It depends a lot on the functionality, for example, glass is more breakable than polycarbonate, but it is easier to clean. There are some discriminants that make the customer choose one material rather than another. Generally, it is the end customer who chooses the material, but it depends on the situation. If there are elements that can come out of the machine, hitting the polycarbonate, they can damage it but not break it. In the case of glass, even if they are tempered and have the film, they can break it. The film allows the glass not to shatter but to sag when it breaks. It can be placed on the inside of the protection, making the glass more shatterproof if hit by something, or inside the glass itself. High Visibility protections are used to make the process visible, to see the machine in operation inside, so that the operator can notice any manufacturing defects. There are customers who prefer to have the protection in stainless steel, but with a porthole to see the process inside. The porthole is a 60/70 cm window positioned at head height, so that the machine can be seen inside. It can be in polycarbonate or glass, the choice of materials is up to the customer, but it depends a lot on the sector of use. DOES A CARTER BECOME OBSOLETE? A Carter does not usually become obsolete, it can wear out if it is in a highly aggressive environment. The guards are often made of stainless steel, a material that rarely loses its protective function over time. It may happen that the guard is wrong, positioned in an unsuitable environment, for example a Carter in a place where dust collects, where easily washable systems should be used instead. For interlocked guards, however, the quantities of use are marked on each component used to monitor the doors or on the safety switches. Obviously, you do not have to count and take into account every time you open and close the door, but you can get an idea of how long the components will last. The hinges and interlocked guards have a micro switch, the Manual will say how many openings it has been tested for, for example 60,000. These are huge numbers, in this case before it gets ruined it would have to be opened for 10,000 days, 5 times a day. It is easier for them to break from a blow. Furthermore, the use of the machine may change, so the door may no longer be needed in that position and will have to be moved. Or in the future the Regulations may change and perhaps a guard in that particular position will no longer be up to standard, thus becoming unreliable. MACHINERY PERIMETER PROTECTIONS: WHAT ARE THEY? Perimeter Protection, in terms of layout and construction choice, is a protection that increases the perimeter of the moving machine. All protections are external to the machinery, but Perimeter Protections go beyond the perimeter of the machine, creating an internal and protected intervention area. With them, a buffer, shock absorber or maintenance area is created that remains separate from the machinery. For example, in the food or pharmaceutical sector there are often glass or polycarbonate cages that prevent you from inserting your hand near the moving part, they are Perimeter Protections. Yellow nets are normally used in machinery with low mechanical or ejection risk, or where forklifts turn, and prevent a person from entering a certain area. In the bottling sector, however, there is often a request to not be hit by objects thrown by the machinery, in which case the fixings must withstand the impact as much as the material. MACHINERY ACCESS STAIRS: HOW TO CHOOSE? The customer always tries to place the stairs and accesses in the most unthinkable places, as the spaces in the plant are often very limited. However, they cannot be built and positioned randomly, there are Technical Standards to be respected. As regards the machinery access stairs, there are different reference gradations. Up to 20° it is a ramp, between 20° and 45° a normal ladder, between 45° and 75° a bunk ladder, while from 85° to 90° a sailor's ladder. All the information on how to choose the access route to the machinery and the characteristics of the various ladders and covers are written in the Technical Standards 14122, which are 4: 14122-1, 14122-2, 14122-3 and 14122-4. The 14122-4 specifies how to make a ladder. It will not have a CE plate as the ladders do not have one, but it must have a plate indicating the weight and the correct use. The 14122-3 concerns the step ladders. In this type of ladder the plate is not necessary. The 14122-2 contains the specifications for the walkable flooring, the cover and the parapet, which must be at least 1.10 m high. The 14122-1 indicates how to choose the access route. These Technical Standards indicate how to build the accesses to the machinery. The 4 Standards cover all access routes and walkable areas at height. According to the Standard on the ladder, the protective cage for the worker must be positioned from 2.20 m up to 3 m. It is not necessary to use a harness on the ladder, as there is a safety cage anyway. In some cases, special handrails are provided, those with hooks for snap hooks, but these are special cases. The ladders at the ladder are a particular access route to the machinery, because you work in a very narrow space. Ramps and bunk ladders are easier to use. PLATFORMS AND FLOORS THAT CAN BE WALKED ON AT HEIGHT ABOVE THE MACHINES: WHAT DO I NEED TO LOOK FOR? The first thing to look at is that the entire walkable perimeter is surrounded by a parapet at least 1.10 m high, a classic railing like those on balconies. Furthermore, there must be a gap in the middle of at least 500 mm. Attached to the railing, all around the perimeter of the walkable area, there must be a heel guard, or a raised area of at least 11 cm. This is to prevent falling or slipping, or to prevent the tools being used from slipping off the platform. The third point to check, which is very important, cannot be seen by eye, as it concerns the capacity of the walkable area, or how much weight it can support per square meter. Normally the calculation is done with 2 operators and a toolbox, and is around 200 kg per square meter. It is absolutely not allowed to climb over the guardrail from the walkable floor and go over the machine. Sometimes you see the maintenance man climbing over it and walking on the channels, this is absolutely not something to do as it is very dangerous. It falls within easily predictable behaviors, in fact if inside the walkable area there is a raised area, or something where the operator can put his foot, it is from that point that the 1.10 m of the parapet is calculated. NEW PROTECTIONS ON OLD MACHINERY: WHO CERTIFIES CE? When talking about old machines that need new protections, a competent person must go and see the machine and interview the worker who uses it. Together with the worker, by interviewing him, you learn the real use of the machine, the good and bad habits, what works well and what should not be done. Based on these interviews, you must do the risk assessment, using Standard 12100, and with the assessment you choose any protections to apply to the machine. Even if the protections were already present in the old machine and only need to be replaced, you must make sure that they are still suitable and justify the confirmation. Then you move on to the installation of the protections, which can be done by the manufacturer or the customer. It is also necessary to check whether what was chosen in the assessment is the same as what was actually installed. Finally, if the construction of the machine dates back to before 1996, it is necessary to make the Declaration of Conformity to Annex V of the Consolidated Law and as specified in Article 11 of Presidential Decree 459 of 1996. If the machine was built after 1996, it has the CE certification, which is not lost. Improving safety does not change the use of the machine, but in any case it is necessary to demonstrate that something has been done well and justify one's choices. SURVEYS DRAWINGS PROTECTIONS FOR OLD MACHINES: WHO DOES THEM? When you have an old machine and you need to apply protections, it is necessary to make some surveys first. It is better to have professionals do them, as the protections must be made to measure. For example, a Carter, if you insert your hand to make an adjustment, must prevent the hand from reaching the other point, therefore it must not be too wide or too narrow. Furthermore, it is also necessary to detect the attachment points, the overall dimensions and the minimum distances from the moving parts, to understand where to position and attach the protections. All the detection activity must be done on the site where the machine is located. These adjustments can also be provided by the customer, but it is normally better for them to be made by the person who builds the protection, because if they are not exact the pieces will not fit. They must therefore be made by a competent person. Once the machine has been detected, a layout is extrapolated, from which the construction drawings are defined. From that moment the design begins, choosing what type of safety devices to put, what type of fixings to use, what type of doors, etc. The type of protection chosen depends on what they have to protect, if High Visibility is important they will have to be made transparent, if we are talking about a machine that does not have expulsion pieces, a metal mesh can be used. We work on the drawings, which will then be sent directly to the workshop for construction. In the meantime, the Technical Office develops the Manual, where each piece is numbered and where there is a diagram to explain the assembly. Along with the Manual there will be a Check List, to check that all the pieces are present. There is a Standard that specifies the requirement for the presence of an Instruction Manual for the machinery. The guards are safety components, they must therefore be CE marked. Be careful because there are those who do not do it, often they are sold as sheet metal and not as safety components.